Since its inception over 50 years ago, inkjet printing has become the most widely adopted method for the reproduction of images and text on paper. Inherently a microfluidic technology, inkjet printing is a process in which individual ink droplets, between 10 to 100 µm diameters, are placed at software-configurable locations on a substrate. The resulting dots can combine to create photo-quality images with resolutions of up to several thousand dots per inch. Such exquisite precision and flexibility make inkjet printing particularly attractive for the scalable fabrication of fine features. Indeed, in addition to coloured inks, this technology has also been adapted to deposit a wide range of materials for manufacturing, including metals, ceramics, polymers, and even biological cells.1
Not surprisingly, the lab on a chip community is also beginning to leverage printing technologies for the fabrication of microfluidic components.2 However, this is not straightforward because the quality of the printed features often depends on the interaction of the ink droplets with the substrate material. Since microfluidic devices are predominantly prototyped using polydimethylsiloxane (PDMS),3 recent research has focused on the development of PDMS-compatible methods for inkjet printing.
In one example, Profs Dachao Li at the Tianjin University, China and Robert C. Roberts at the University of Hong Kong used inkjet printing to form robust silver microelectrodes on PDMS-based microfluidics for glucose sensing.4 In forming these electrodes, the PDMS material posed two challenges: 1) poor adhesion of silver to PDMS inhibited robust electrode formation and, 2) the inherent hydrophobicity of PDMS promoted coalescence of neighboring ink droplets, which impaired the precision of printed features.
To overcome these challenges, the researchers modified the substrate using (3-Mercaptopropyl)trimethoxysilane, a coupling reagent that presents thiol groups on the PDMS surface. The thiol groups not only served as covalent anchoring sites for the inkjet-printed silver but also increased the wettability of the ink droplet, which improved the precision of the printed features.
Remarkably, the printed electrodes formed on these substrates tolerated very harsh stress tests, including immersion in water, exposure to high pressure air stream, and even ultrasonication. This new fabrication strategy enabled the team to create an all-in-one PDMS system with fluid handling and a three-electrode electrochemical cell for transdermal detection of glucose (Picture 1).
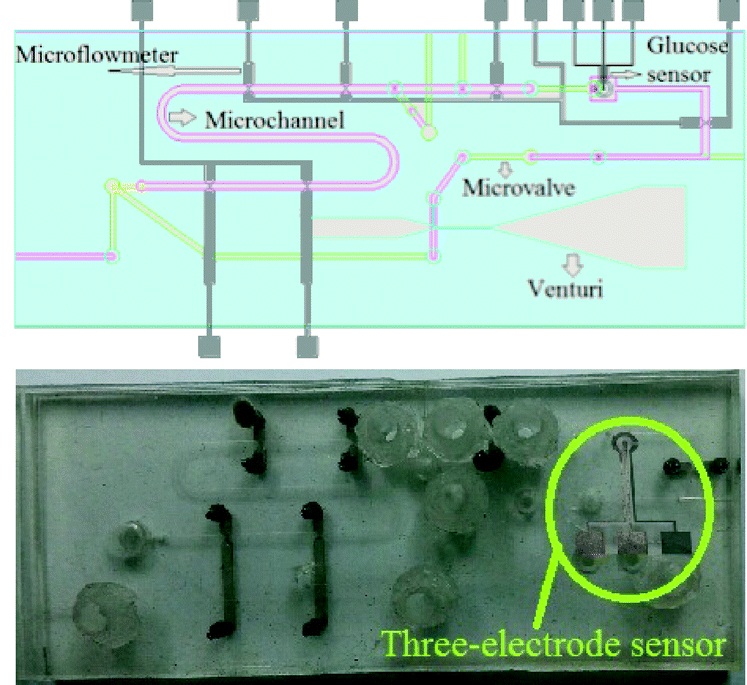
In another example, Profs Yanlin Song and Fengyu Li at the Chinese Academy of Sciences, China developed an elegant inkjet-printed method 5 for the fabrication of enclosed PDMS microchannels. This process conventionally requires at least 4 steps: 1) create a solid template via photolithography, 2) cast PDMS prepolymer mixture in the template, 3) cure and separate the PDMS from the template, and 4) bond the molded PDMS to a substrate.
To simplify this procedure, the researchers implemented a liquid template formed by inkjet-printing (Picture 2). Here, an immiscible liquid pattern is printed directly on a pool of PDMS prepolymer solution. Within seconds, the liquid spontaneously submerges below the prepolymer solution and acts as a template. Upon heating, the polymer solidifies while the liquid template evaporates, leaving behind an enclosed PDMS microchannel device.
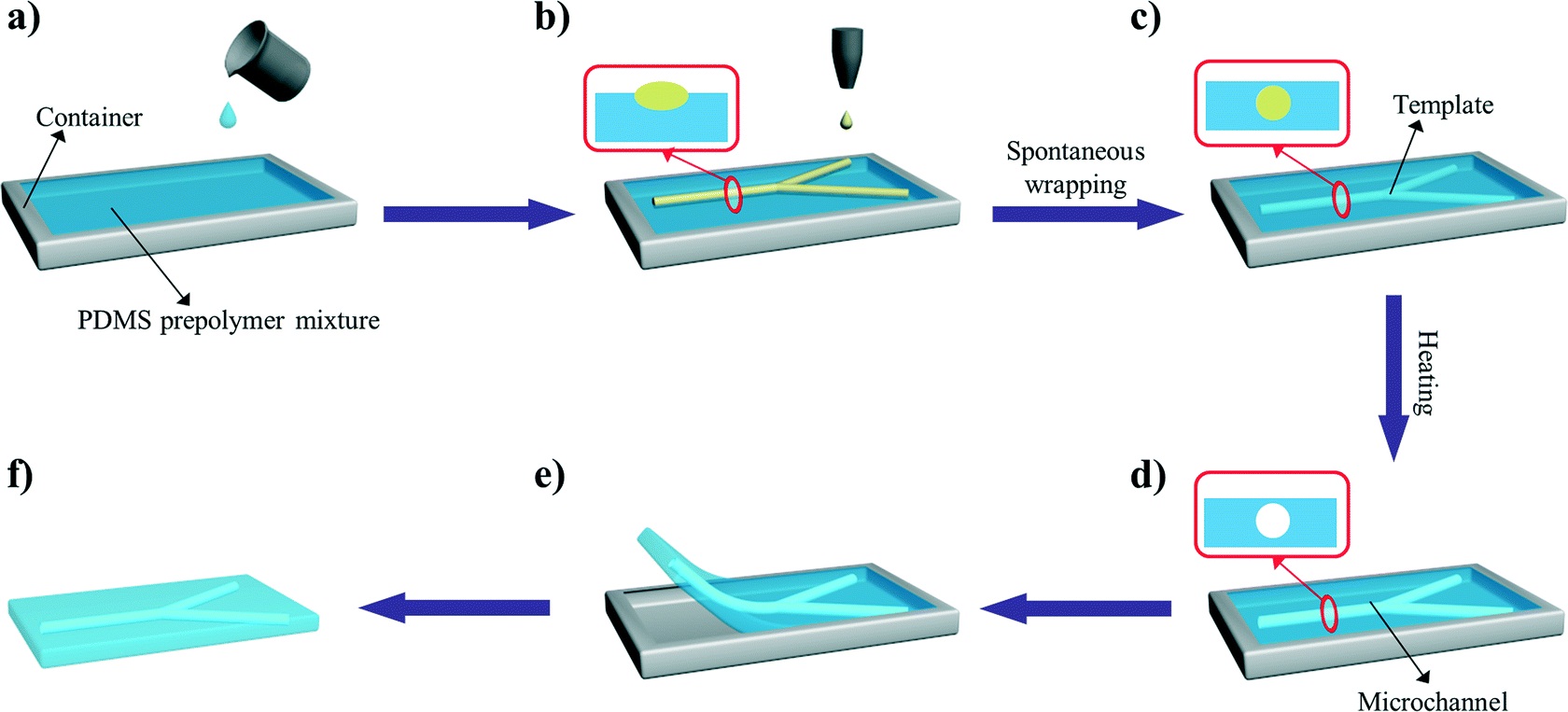
In the development of this method, one major challenge was maintaining the stability of the liquid template in the prepolymer solution. Due to surface tension, printed liquid templates tend to break up and relax into discontinuous spherical droplets. Although this instability can be inhibited by increasing the liquid viscosity, high viscosities are not compatible with inkjet printing. To address this challenge, the researchers used an ink whose viscosity is tunable by temperature. At room temperature, the ink has relatively low viscosity (10 centipoise), which is compatible with inkjet printing. When the ink is printed on a cooled (3-4oC) pool of prepolymer solution, the viscosity of the liquid increases dramatically (>40 centipoise), which enabled the formation of a stable liquid template with no breakages.
This inkjet-printed approach enabled the formation of remarkably versatile PDMS microchannels. The diameters of the fabricated channels can range from 100 to 900 µm just by changing the template design. In addition, the interior surface of the channel can be modified by including vinyl-terminated functional molecules in the ink composition, which covalently incorporates in the PDMS matrix during thermal curing. Applying this technique with vinyl-terminated poly(ethylene glycol)methacrylate molecules, the researchers effortlessly imbue their devices with protein fouling resistance.
In summary, the lab on a chip community is beginning to leverage the benefits of inkjet printing in the fabrication of microfluidic components. By engineering the interaction of the ink droplets with the substrate material, researchers are devising innovative ways to fabricate robust electrodes and versatile microchannels without the need for cleanroom facilities and complicated procedures.
1. I. M. Hutchings and G. D. Martin, Inkjet technology for digital fabrication, John Wiley & Sons, 2012.
2. P. Tseng, C. Murray, D. Kim and D. Di Carlo, Lab on a Chip, 2014, 14, 1491-1495.
3. E. Berthier, E. W. K. Young and D. Beebe, Lab on a Chip, 2012, 12, 1224-1237.
4. J. Wu, R. Wang, H. Yu, G. Li, K. Xu, N. C. Tien, R. C. Roberts and D. Li, Lab on a Chip, 2015, 15, 690-695.
5. Y. Guo, L. Li, F. Li, H. Zhou and Y. Song, Lab on a Chip, 2015, 15, 1759-1764.