In the ever-evolving landscape of materials engineering, researchers are pushing the boundaries of sustainability and functionality. One groundbreaking avenue of exploration is the integration of mycelium, the root-like structure of fungi, into biocomposites. In this blog post, we delve into a recent study that harnesses the unique properties of mycelium through 3D printing and indirect inoculation, resulting in a material with enhanced mechanical strength and diverse applications.
Shen et al. formulated a biocomposite designed to offer mechanical robustness and compatibility with mycelium. To achieve this, the researchers ingeniously selected chitosan and cellulose and introduced leftover coffee grounds as a sustainable source of nutrients. This careful combination created a material that not only exhibited shear thinning behavior, ideal for 3D printing but also laid the foundation for mycelium colonization (Figure 1).
One distinguishing feature of this study is the use of indirect inoculation for mycelium colonization. Traditionally, direct inoculation involves mixing the inoculum with the composite material before printing. However, the researchers chose a different route, incubating printed samples on a bed of live mycelium. This indirect approach, although taking longer for full colonization, turned out to be more effective.
The study of the mechanical properties of biocomposites revealed a strong influence on the orientation of the 3D printing tool path and the alignment of the cellulose fibers. The authors printed parts of different shapes, and the mechanical properties were dependent on the printing design. However, the fully colonized material showed a notable increase in mechanical strength, surpassing previously reported mycelium composites.
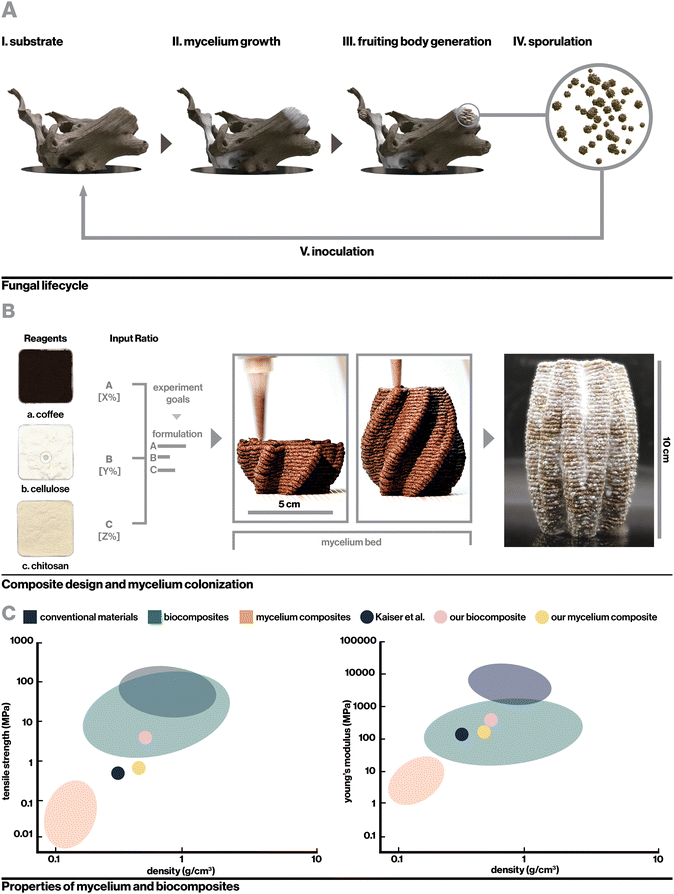
Figure 1. (A) Keeping the solid:liquid ratio consistent, the introduction of spent coffee grounds augmented the rate of mycelium colonization up to a threshold (B) The optimized biocomposite displays shear-thinning characteristics, offering advantages for extrusion-based additive manufacturing. (C) Achieving a vertical resolution of approximately 2 mm. Adapted from DOI: 10.1039/D3MH01277H with permission from the Royal Society of Chemistry
The influence of mycelium extended beyond mechanical properties to wettability and absorption characteristics. The fully colonized composite developed a smooth hydrophobic “skin,” demonstrating improved water contact angles. Under submerged conditions, the colonized compound demonstrated lower water absorption and volume swelling, attributed to the presence of hydrophobic mycelial hyphae.
The team explored the capabilities of mycelium to develop biosealed mycelium containers as self-sealing living boxes and the creation of flexible textile-like materials through precise 3D printing and mycelium colonization. By printing biocomposite panels with consistent gaps and allowing mycelium to cover them, flexible hinges were formed, enabling the creation of a material capable of bending and stretching in multiple directions.
In conclusion, the fusion of 3D printing, indirect inoculation, and mycelium colonization represents a leap forward in the field of sustainable biocomposites. The mechanical properties, wetting characteristics, and adaptability of the biocomposite open avenues for green alternatives in packaging, textiles, and more.
To find out more, please read:
Robust myco-composites: a biocomposite platform for versatile hybrid-living materials
Sabrina C. Shen, Nicolas A. Lee, William J. Lockett, Aliai D. Acuil, Hannah B. Gazdus, Branden N. Spitzerab and Markus J. Buehler
Mater. Horiz., 2024, Advance Article, DOI: 10.1039/D3MH01277H
About the blogger
![]()
Dr. Danila Merino is the PI of the SusBioComp group at POLYMAT and a Materials Horizons Community Board member. Her research focuses on the development of new sustainable biocomposite materials derived from biomass specifically designed to protect and enhance agricultural and food systems with minimal environmental impact. |