Additive manufacturing is a polymer processing method enabling the preparation of 3D architectures with a high level of design freedom. While some of the additive manufacturing technologies, such as fused deposition modeling (FDM) are commonly used at an industrial level for prototyping, there are still numerous challenges to tackle for achieving a 3D architecture that possesses state-of-the-art thermomechanical properties, compared to those obtained via conventional methods. Considering the sustainability aspect of the selected additive manufacturing method, including the management of the failed 3D parts, is also of utmost importance in the context of sustainable laboratories.
As recently reported by Jiang et al., there are additional challenges for the additive manufacturing of continuous fiber composites which are made of a carbon fiber that is surrounded by a polymer matrix. FDM is often used to prepare such samples, where the continuous carbon fiber and the thermoplastic filament are fed separately during the processing of the materials. While this strategy works to produce continuous fiber composites, the resulting mechanical properties are mostly dictated by those of the thermoplastic polymer. To optimize the mechanical properties of such samples, an interesting alternative strategy consists of using a thermoset polymer matrix processed via direct-ink writing (DIW). While some successes have been reported exploiting DIW, the rheological properties of the thermoset in the pre-printing stage needs to meet specific requirements to enable the extrusion of the formulation, including shear-thinning and thixotropy. The solidification kinetics of the thermoset formulation occurring upon exposure of the 3D printed formulation to heat is usually slow and leads to a uniform curing, but also leads to difficulties in obtaining a 3D printed architecture with a high level of post-treatment print fidelity. To circumvent this problem, UV curable resins, once again printed via direct-ink writing, can be used as a polymer matrix for the continuous fiber composite as their solidification kinetics are often faster than those of thermosets. While this process is efficient, the presence of the continuous fiber may impede the penetration of the irradiation, usually leading to a fast yet non-uniform curing.
To address the challenges involved in the preparation of continuous fiber composites linked to the DIW of either the thermoset or the UV curable resin, Jiang et al. designed a formulation capable of undergoing a two-stage curing process, therefore successfully combining the advantages of both UV curing (fast solidification) and heat-based curing (uniform curing). They combined the 2-hydroxy-3-phenoxypropyl acrylate monomer, the phenylbis (2,4,6-glycerolate diacrylate) photoinitiator, and a triazabicyclodecene as the bond exchange reaction catalyst. As illustrated in Figure 1, the first stage (UV irradiation) allows for the free-radical polymerization to occur while the second stage (heat) is used to increase the resulting material’s crosslinking density via the transesterification reactions occurring between the hydroxyl and the ester functional groups of the material.
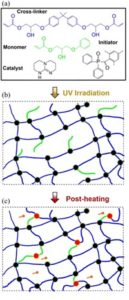
Figure 1. a) Chemical structures composing the two-stage curable resin undergoing b) UV curing and c) heating illustrating the bond exchange reaction involved in the optimization of the thermomechanical properties of the 3D printed architectures. Reproduced from DOI: 10.1039/d3mh01304a with permission from the Royal Society of Chemistry.
This transesterification, also referred to as bond exchange reaction, is crucial to optimize the thermomechanical properties of the 3D printed continuous fiber composites, which results in high performance applications for these architectures. Jiang et al. reported not only a ~11-fold increase in the modulus of the two-stage cured samples compared to the UV cured only samples, but also a better adhesion (referred to as welding) between the layers deposited on top of one another. This enhanced adhesion is a consequence of the covalent bond created between the layers upon the heating step which is, once again, facilitated by the bond exchange reaction.
The capability of the 3D printed architectures to undergo bond exchange reaction also allows for the repairing and reshaping of the architectures. It was shown that the 3D printed architectures could be recycled via depolymerization in ethylene glycol at high temperature (160°C), which is an important asset for a thermoset based composite, especially in the context of sustainable materials and processing. This proof-of-concept has been extended to acrylate/epoxy-based commercial resins, opening the door to fundamental studies of the mechanisms of bond exchange reactions in similar resins where further understanding of the structure-processing-property relationships could be established to lead to the rational design of custom resins for the 3D printing of continuous fiber composites.
To find out more, please read:
3D Printing of continuous fiber composites using two-stage UV curable resin
Huan Jiang, Arif M. Abdullah, Yuchen Ding, Christopher Chung, Martin L. Dunn and Kai Yu
Mater. Horiz., 2023, 10, 5508-5520, DOI: 10.1039/D3MH01304A
About the blogger
![]()
Audrey Laventure is an assistant professor in the Department of Chemistry at the Université de Montréal (UdeM), QC, Canada, and a member of the Materials Horizons Community Board. Since 2021, she holds the Canada Research Chair in Functional Polymer Materials. Her expertise lies at the intersection of physical chemistry, polymer processing and advanced materials characterization. In 2023, Audrey was selected to lead the molecular materials axis of the new Institut Courtois at UdeM. Audrey was also part of the first Youth Council of the Chief Science Advisor of Canada (2020-2023) and the Science Meets Parliament 2023 cohort.
|